Keys toward precise attitude control
Authored by Austin Chang, 2021.05.04
Revised by Afan Huang, 2024.10.07
In the complex world of satellite engineering, the Attitude Determination and Control System (ADCS) plays a crucial role in maintaining a satellite's orientation and stability. However, ADCS failures can manifest in various ways, from steady-state errors and prolonged response times to divergent control outcomes. While improper calibration of attitude sensors and actuators, along with misalignment between sensor, actuator, and system reference frames, are often culprits, two significant factors often fly under the radar: inaccurate mass properties and insufficient tuning of the attitude control system. (as illustrated in Figure 1)
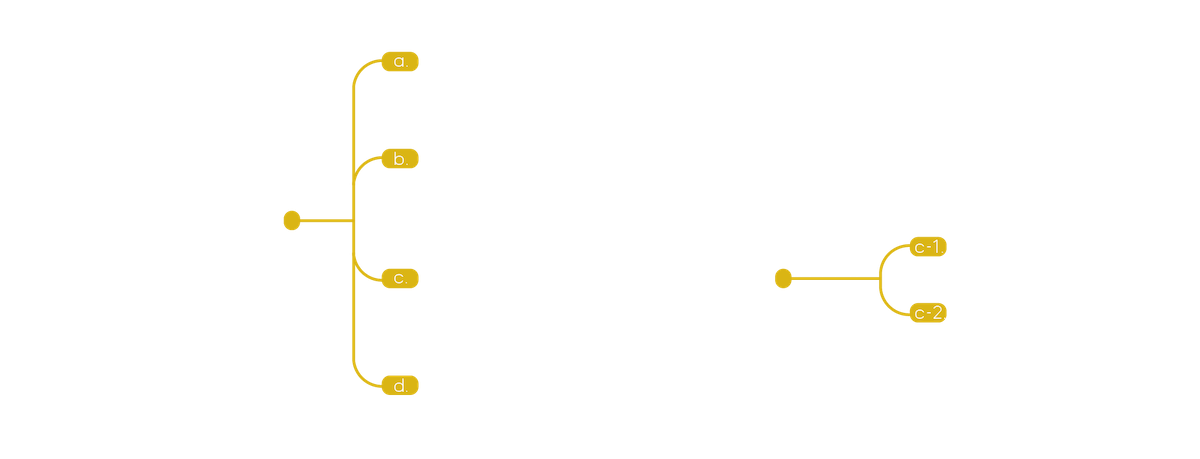
Figure 1. Factors for the failure of the attitude control system
Underpinning these issues lie the satellite's mass properties - critical mechanical characteristics that include total mass, center of mass (COM), moment of inertia (MOI), and product of inertia (POI). These properties, particularly the combination of MOI and POI forming the "inertia matrix" or "inertia tensor," are fundamental to effective attitude control. This concept is so central to our work that it inspired our company's name. When developing or integrating an ADCS, accurately defining these parameters is not just beneficial - it's essential. They form the backbone of proper attitude control algorithm propagation, ensuring that the satellite can maintain its intended orientation with precision.
Typically, engineers obtain mass properties through simulations using sophisticated Computer-Aided Design (CAD) tools like SolidWorks or Autodesk. However, the transition from simulation to reality is not always smooth. Two types of errors can emerge in practice: variations in mass properties over time Figure 1 (c-1) and discrepancies between simulation results and the physically integrated hardware Figure 1 (c-2).
First, we encounter variations in mass properties over time, as illustrated in Figure 1 (c-1). These changes can stem from factors such as thermal variation, which causes satellite deformation due to differing thermal expansion coefficients across materials. Additionally, flexible components like solar panels can significantly alter mass properties during a satellite's operational life. The second type of error manifests as discrepancies between simulation results and the physically integrated hardware, shown in Figure 1 (c-2). This gap arises from a multitude of factors: inconsistencies in material densities, machining tolerances, assembly errors, and other unpredictable elements. These variables can cause the actual moment of inertia and center of mass to deviate significantly from CAD-based calculations.
To address these challenges, a two-pronged approach is necessary. For the second issue – the simulation-reality gap – obtaining accurate measurements of your assembled satellite's mass properties is crucial. This data provides a real-world baseline that can dramatically improve the accuracy of attitude control systems. Dealing with the first issue – temporal variations – often requires embedding robust control techniques into the satellite's control logic. Interestingly, our experience suggests that this issue becomes truly significant only for larger satellites, where the characteristics of flexible bodies dominate the spacecraft's behavior.
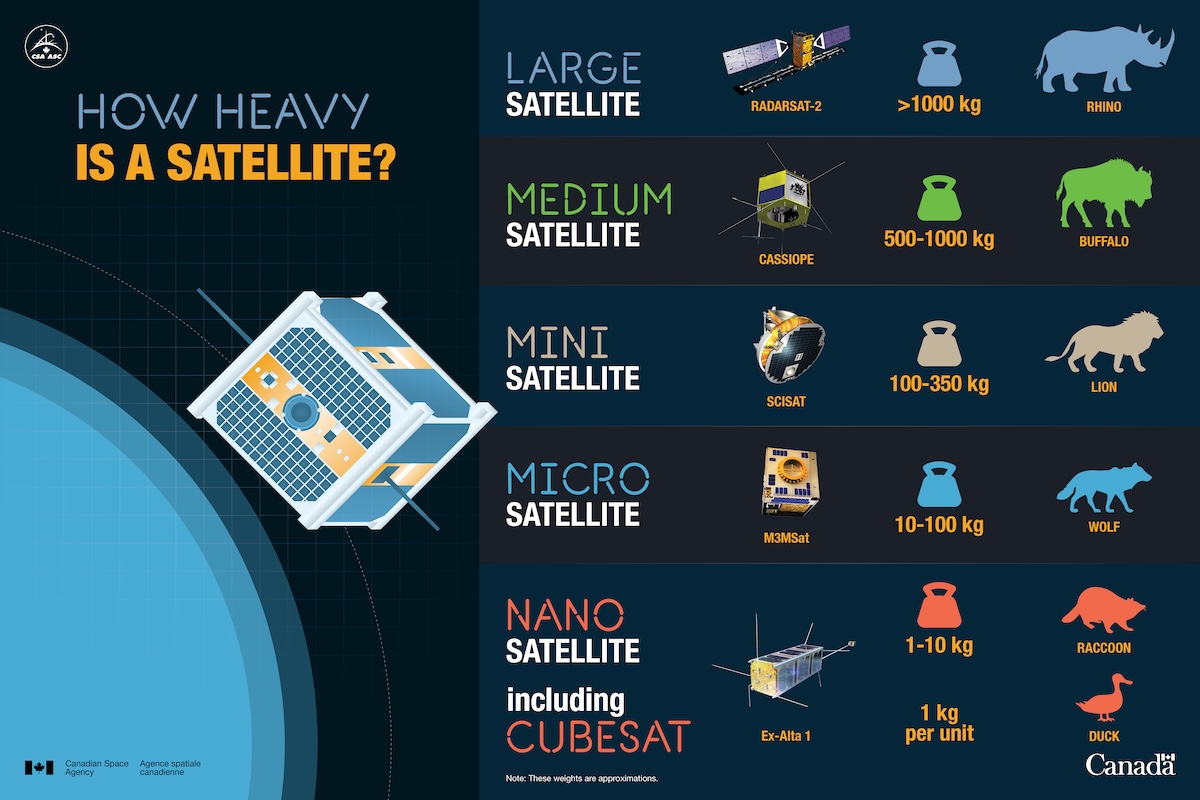
Figure 2. The mass of satellites in five categories (3)
(The mini and medium satellites are categorized as small satellites.)
Recognizing the critical need for accurate mass property measurements, especially for smaller spacecraft, Tensor Tech has developed the TensorTestBed, an attitude determination and control system testbed as Figure 3 shows. The TensorTestBed stands out in a market where most mass property measurement instruments are calibrated for objects weighing over 30kg. Our focus on nano-satellites fills a crucial gap in the industry, providing precise measurements for these increasingly popular smaller spacecraft.
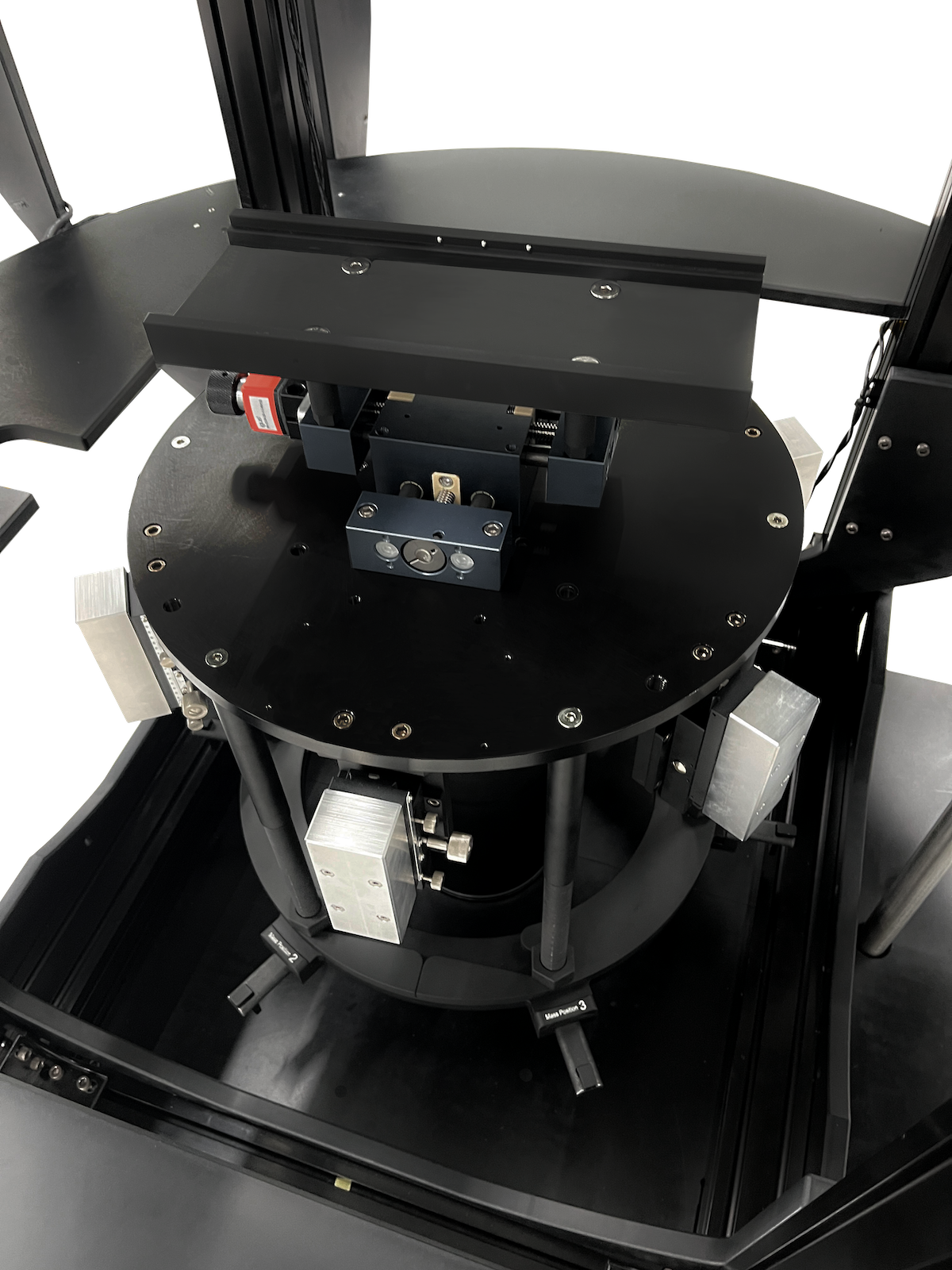
Figure 3. TensorTestBed, the satellite mass properties measurement and attitude control testing facility developed by Tensor Tech
Lastly, to resolve the issue highlighted in Figure 1(d), the TensorTestBed offers an effective solution for both our clients and internal teams to test the performance of their attitude control systems. Featured with a hemispherical air-bearing platform, the TensorTestBed provides one of the most accurate ways to simulate attitude control in a near zero-gravity environment on Earth. Without access to such specialized equipment, many struggle to properly tune their attitude control systems, resulting in suboptimal performance.
References
1. Space Electronics, LLC. (2008). HOW MASS PROPERTIES AFFECT SATELLITE ATTITUDE CONTROL. https://raptor-scientific.com/content/uploads/2020/12/MPAffectSatelliteAttitudeControl.pdf
2. Jose Luis Redondo Gutiérrez. (2019). Attitude control of flexible spacecraft. https://elib.dlr.de/126439/1/Gutierrez%20-%20Attitude%20control%20of%20flexible%20spacecraft.pdf
3. What is a CubeSat. (2018). Canada.Ca. https://www.asc-csa.gc.ca/eng/satellites/cubesat/what-is-a-cubesat.asp